Manufacturer of PTN Series Ring Die for Pellet mill spare parts
- SHH.ZHENGYI
● PTN series ring die
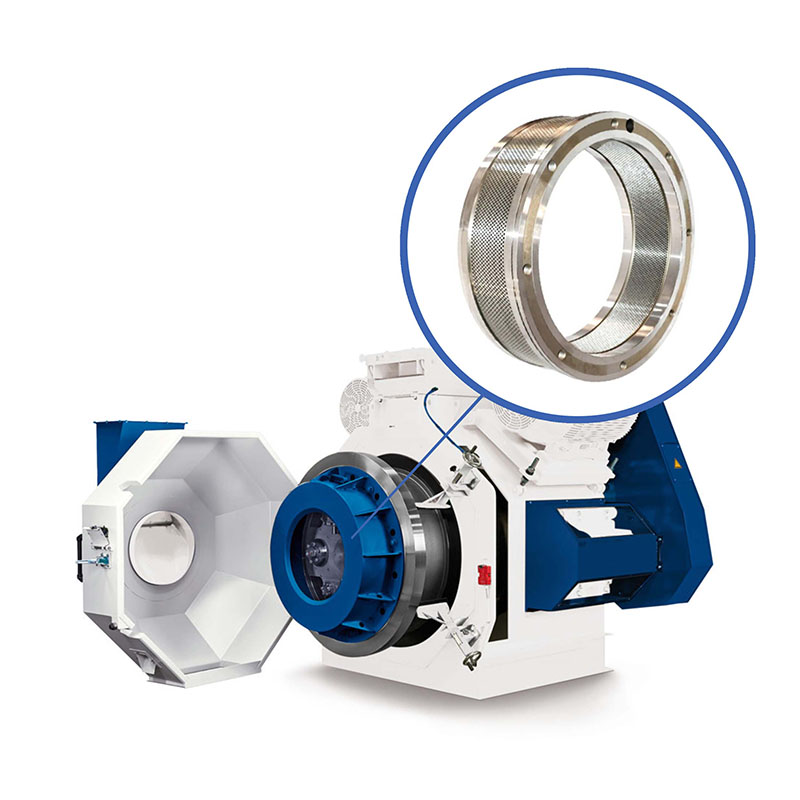
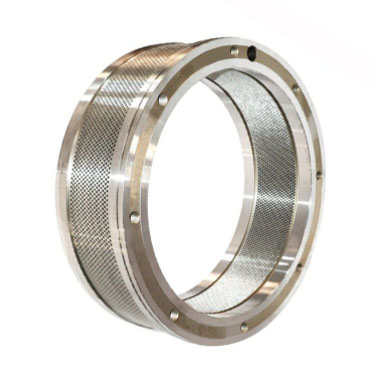
PTN pellet mill series ring die is made of high-quality alloy steel or high-chromium stainless steel (German standard X46cr13). It is processed by forging, cutting, drilling, heat treatment and other processes. Through strict production management and quality system, the hardness, die hole uniformity and die hole finish of the production ring die have reached very high quality.
Parameter
S/N | Model | Size OD*ID*overall width*pad width -mm | Hole size mm |
1 | PTN450 | 560*450*180*106 | 1-12 |
2 | PTN580 | 680*580*216*140 | 1-12 |
3 | PTN650 | 791*650*245*175 | 1-12 |
Analysis of Abnormal Situation and Recommended Improvements
Reason Analysis for Broken (normally occurred in
continuous casting of small enterprises)
1. Die broken by drive wheel matching surface
2. Die broken by wearing and deformation of die lining ring.
3. Die broken by waring of driving key.
4. Indentation impressed on the surface of the die for the weakening effect of the de-ironing device, and then cause die to crack.
5. Small opening between the die and the compression roller.
6. Die broken by small compression ratio, small diameter fish feed dies without pressure-relief vent.
No. | Appearance | Reasons | Solutions |
1 | Particle bends, with cracks |
|
|
2 | With transversal crack |
|
|
3 | Vertical cracks |
|
|
4 | Radiative cracks | Large particles exist (half an oorn or whole corns left) | Control the fineness of raw materials, increase grinding evenness. |
5 | Surface unevenness |
|
|
6. | Whisker like pellet | Too much steam and too large pressure, pellet cracks when left the die. | 1. Reduce steam pressure, use low-pressure steam (15 – 20psi)for conditioning. 2. Check the position of the reducing valve. |
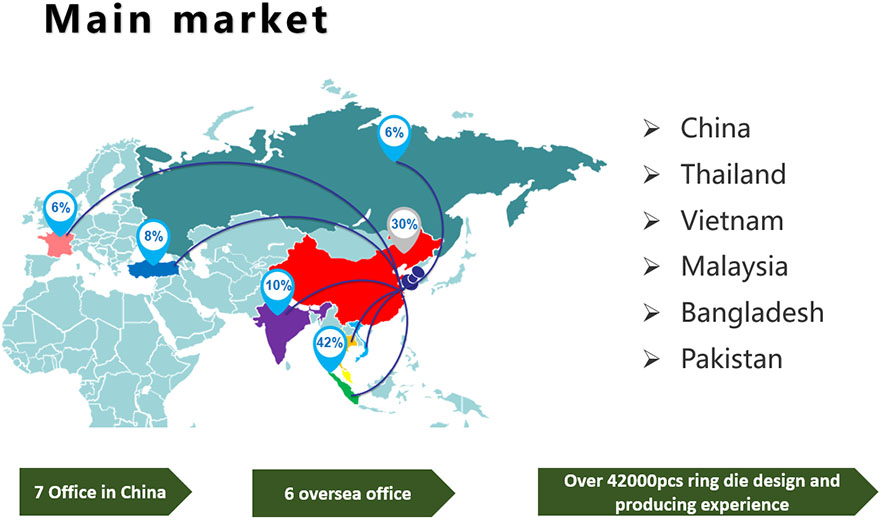
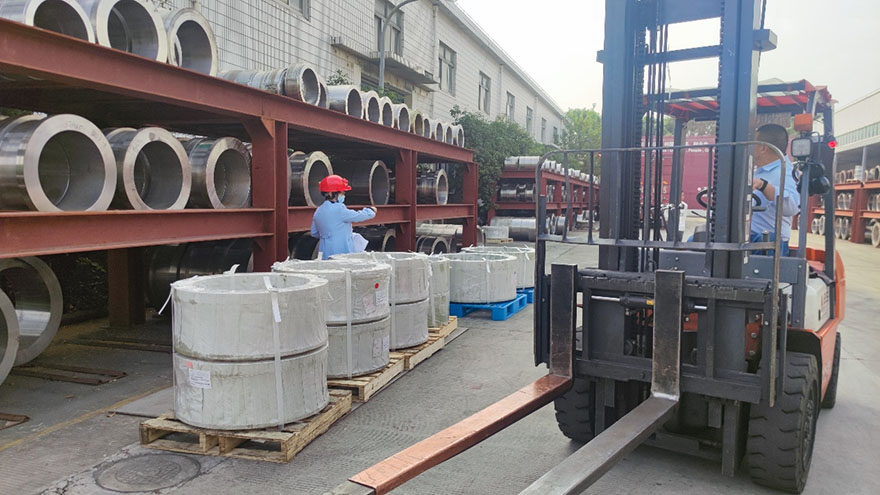