SZLH series pellet mill ring die
- SHH.ZHENGYI
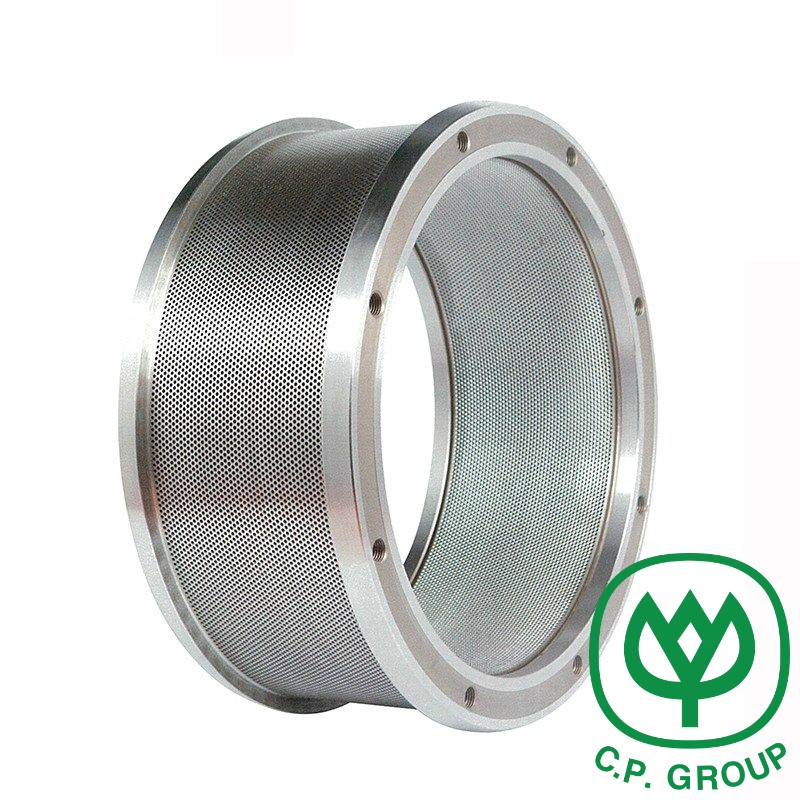
1.Select high-quality raw materials, secondary steelmaking, degassing billet;
2.Ring die material: X46Cr13 / 4Cr13 (stainless steel), 42Crmo / 20CrMnTi (alloy steel) or other custom materials;
3.Imported gun drill and multi-station drill, one-time forming die hole, high-quality finish, production of feed, beautiful appearance and high output;
4.Select the combination of vacuum furnace and continuous quenching furnace to ensure long service life;
5.According to the principle and requirements of the customer to design compression ratio and strength;
6.Microscopic examination to ensure product quality;
42Crmo / 20CrMnTi alloy steel ring die processing technology:
Cutting→Forging→Normalizing→Roughing→Tempering→Finishing→Drilling (Expanding) Hole→Carburizing→Grinding→(Excluding Oxidation Layer) →Pressure Testing→(Phosphorus Passivation)→Coating Antirust Oil→Check and save options;
X46Cr13 / 4Cr13 stainless steel ring die processing technology:
Cutting→Forging→Roughing→Normalizing→Finishing→Quenching and tempering→ › Finishing→Drilling hole→Nitriding→Polishing→Pressure test→ Coating resistance→Rusty oil→Check and save options;
S/N |
Model |
Size OD*ID*overall width*pad width -mm |
Hole size mm |
1 |
SZLH320 |
432*320*130*87 |
1-12 |
2 |
SZLH350 |
500*350*180*100 |
1-12 |
3 |
SZLH400 |
558*400*200*120 |
1-12 |
4 |
SZLH400D |
558*400*218*138 |
1-12 |
5 |
SZLH420 |
580*420*196*120 |
1-12 |
6 |
SZLH420D |
580*420*214*140 |
1-12 |
7 |
SZLH508 |
660*508*238*155 |
1-12 |
8 |
SZLH508E |
660*508*284*185 |
1-12 |
9 |
SZLH558 |
774*572*270*170 |
1-12 |
10 |
SZLH578 |
774*572*300*200 |
1-12 |
11 |
SZLH768 |
966*761*370*210 |
1-12 |
Stepped roller shell
The roller shell is one of the main working parts of pellet mill. Used to process various biofuel pellets, animal feed and other pellets. Using high wear-resistant alloy steel (40Cr, 20Crmnti, Gcr15), carburizing heat treatment, uniform hardness. The service life is long, and there are different types of structures such as tooth-shaped through-shaped, tooth-shaped blocked, and hole-shaped. The pressing roller part is made of internal eccentric shaft and other parts with precise dimensions, which is convenient to adjust the distance between the pressing roller and the ring die according to the user’s production requirements, and it is easy to fold and install, and it is easy to replace the pressing roller shell.
Precautions:
1. Correctly select the appropriate die hole compression ratio;
2. Correctly adjust the working gap between the ring die and the pressure roller to be between 0.1 and 0.3mm (the pressure roller is driven by the ring die after the new granulator is turned on in a “like rotating but not rotating” state);
3. The new ring die should be used with a new pressure roller, and the pressure roller and the ring die must be loose before and then tightened. When sharp corners appear on both sides of the pressure roller, the flange of the pressure roller should be smoothed with a hand grinder in time to facilitate a good fit between the pressure roller and the ring die;
4. The raw material must undergo preliminary cleaning and magnetic separation before the pelletizer to reduce iron pressing into the die hole. And to check the die hole regularly to see if there is any blockage. Punch out or drill out the blocked mold hole in time;
5. Plastic deformation of the guide cone hole of the ring die should be repaired. When repairing, it should be noted that the lowest part of the working inner surface of the ring die should be 2mm higher than the bottom of the overtravel groove, and there is still room for adjusting the eccentric shaft of the pressure roller after repair Otherwise, the ring die should be scrapped;
6. The pressure roller shell is made of wear-resistant alloy material by gold processing and heat treatment. The tooth surface form of the pressure roller shell has a certain influence on the granulation performance.
Commonly used roller shell tooth profile: tooth profile through type, tooth profile not through type, hole type.
1. Pass and tooth groove rollers are mainly used for pelletizing livestock and poultry materials. The advantage of pass rollers is that the ring die wears evenly, but the coil performance is poor.
2.The tooth groove shape pressure roller has good coil material performance and is commonly used in feed factories, but the wear of the ring die is not uniform. The tooth groove shape pressure roller with sealing edge is mainly suitable for the pelletizing of aquatic materials. Slide on both sides.
HELICAL ROLLER SHELL
The roller shell is one of the main working parts of pellet mill. Used to process various biofuel pellets, animal feed and other pellets. Using high wear-resistant alloy steel (40Cr, 20Crmnti, Gcr15), carburizing heat treatment, uniform hardness. The service life is long, and there are different types of structures such as tooth-shaped through-shaped, tooth-shaped blocked, and hole-shaped. The pressing roller part is made of internal eccentric shaft and other parts with precise dimensions, which is convenient to adjust the distance between the pressing roller and the ring die according to the user’s production requirements, and it is easy to fold and install, and it is easy to replace the pressing roller shell.
Precautions:
1. Correctly select the appropriate die hole compression ratio;
2. Correctly adjust the working gap between the ring die and the pressure roller to be between 0.1 and 0.3mm (the pressure roller is driven by the ring die after the new granulator is turned on in a “like rotating but not rotating” state);
3. The new ring die should be used with a new pressure roller, and the pressure roller and the ring die must be loose before and then tightened. When sharp corners appear on both sides of the pressure roller, the flange of the pressure roller should be smoothed with a hand grinder in time to facilitate a good fit between the pressure roller and the ring die;
4. The raw material must undergo preliminary cleaning and magnetic separation before the pelletizer to reduce iron pressing into the die hole. And to check the die hole regularly to see if there is any blockage. Punch out or drill out the blocked mold hole in time;
5. Plastic deformation of the guide cone hole of the ring die should be repaired. When repairing, it should be noted that the lowest part of the working inner surface of the ring die should be 2mm higher than the bottom of the overtravel groove, and there is still room for adjusting the eccentric shaft of the pressure roller after repair Otherwise, the ring die should be scrapped;
6. The pressure roller shell is made of wear-resistant alloy material by gold processing and heat treatment. The tooth surface form of the pressure roller shell has a certain influence on the granulation performance.
Commonly used roller shell tooth profile: tooth profile through type, tooth profile not through type, hole type.
1. Pass and tooth groove rollers are mainly used for pelletizing livestock and poultry materials. The advantage of pass rollers is that the ring die wears evenly, but the coil performance is poor.
2.The tooth groove shape pressure roller has good coil material performance and is commonly used in feed factories, but the wear of the ring die is not uniform. The tooth groove shape pressure roller with sealing edge is mainly suitable for the pelletizing of aquatic materials. Slide on both sides.